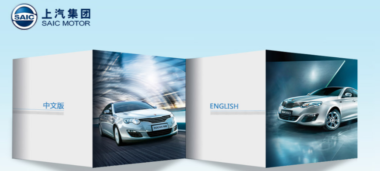
仿真分析是汽车碰撞安全性研究的重要手段。在汽车被动安全性整车仿真分析中,常用的有限元仿真分析求解器软件有 LS-DYNA、RADIOSS、 PAM-CRASH、ABAQUS 等。整车被动安全性研究是汽车研发领域中的重点,工程实际中经常遇到不同软件有限元模型之间的转化问题。
针对上海汽车某项目,探讨某轿车从LS-DYNA 向RADIOSS 的转换方法,然后针对 RADIOSS 格式的模型仿真分析结果与工程上的应用,利用整车64KPH 偏置碰、50KPH 全宽正碰、以及50KPH 的可移动变形壁障等试验测试数据进行了比较。验证了 RADIOSS 求解器计算结果的在工程上的可行性,以及与试验结果的一致性。
挑战
整车碰撞模型主要包括白车身、座椅、底盘、转向、动力总成等结构。针对不同的碰撞规则,又带有可移动壁障、固定壁障以及刚形体台车等。整车有限元模型,节点总数为 1289275,单元总数为 1332879,其中壳单元总数为1280025,实体单元总数为 40606,一维单元总数为 12248,二维单元的平均尺寸为 8mm。
解决方案
软件自动转换
在对其轿车碰撞安全性研究过程中,以此轿车完善的整车碰撞有限元模型为基础,进行从 LS-DYNA 格式到RADIOSS 格式的转换。
首先,打开HyperWorks 的HyperCrash 模块,选择RADIOSS 格式,导入LS-DYNA 格式的整车子模型文件。导入成功后,采用 Model Checker 功能对模型进行初步的检查,查看转化成 RADIOSS 格式的模型是否有错误,并检查 Warning 信息主要内容,然后再将此模型用指定的 RADIOSS 格式导出,形成*.RAD 文件,从而实现模型文件格式上的自动转换。
LS-DYNA 代码格式默认为每行 80 个有效字符,RADIOSS 代码格式则默认是每行 100 字符,且控制卡片的组合形式均不一样。自动转换过程可以将模型的PART、NODE、ELEMENT 等信息的格式,以及常用的零部件材料特性、厚度特性的基本格式转换为相应的模式。通过软件自动转换过来的基本参数格式一致,但是二者之间的转换仍存在不能完全自动实现的情况,这些情况需要通过手动方式进行调整。
材料模型和单元的属性
由于LS-DYNA 和RADIOSS 对零部件的材料和单元属性的定义方式不同,计算时对应的各项更佳参数也不同,需要手工调整的内容主要有材料的各项参数、单元属性各项参数。
对于具体的材料参数的设定,在本次模型转换中,选用了在不同应变速率下定义多个应力应变曲线的方法。
整车模型中常的转动副、阻尼、弹簧、球铰,以及焊点、包边、粘胶等特征,在LS-DYNA 和RADIOSS 中均用一维单元来模拟,其区别在于 LS-DYNA 格式的模型将分别对一维单元赋予单元属性卡片和材料属性卡片,而RADIOSS 格式的模型中,一维单元的所有属性均通过一张卡片来实现,其中还包含所有可能的失效方式,不需要再单独赋予其材料特性。
焊点和刚体连接
在 LS-DYNA 中,焊点的定义是通过 beam 一维单元及其两个节点与相关零部件之间的 tie 接触来实现的。在RADIOSS 中,焊点的定义是通过spring beam 一维单元,同时对于每组spring beam 单元的上下节点分别与对应的零部件生成一个type2 接触来实现的。
本模型中,刚体的属性体现在RBODY 中,如发动机、变速器刚体的属性,如质心、转动惯量等,其材料选用普通的弹性体材料,目的在于体现带网格的刚体与周围零部件发生接触时的有效接触刚度。对于螺栓形式的刚性体连接,LS-DYNA 和RADIOSS 均可以对相应零部件采用rigid body 来实现。对于刚性体与刚性体之间的连接,如子模型之间的连接,在 LS-DYNA 中,各子总成之间的连接均通过刚性片以及*CONSTRAINED_RIGID_BODIES 控制卡片将两个刚体连接在一起。而在RADIOSS 中,则采用一个RBODY,所选择的节点通过group by part 的形式将两个片体的所有node 组合在一起,从而实现将两个刚性片连接在一起,而这两个片体均设置为弹性体材料。
边界条件的加载
整车模型边界条件的加载包含整车基本模型、壁障的加载及相关设置、整车自接触以及与壁障/地面之间的接触设置、整车模型需要重点研究的截面力、加速度、应力、应变以及零部件能量变化等信息要求的设置和输出。不同软件均有其独自的设置方式,且相关的控制参数均具有其软件包含的独自的特性。
模型计算的控制卡片
模型转换时,HyperCrash 会自动生成一个求解计算的 engine 控制文件,根据不同的要求对求解计算控制参数进行详细设定,主要包括计算时间、计算步长控制、输出信息的类别设定等。LS-DYNA 与RADIOSS 的不同之处在于,前者可以单独给予各项时间历程数据信息不同的输出方式和输出时间间隔,而后者对所有的时间历程数据信息只能采用相同的输出方式和输出时间间隔。RADIOSS 可以通过不同的engine 文件对模型进行各个时间段的独立求解。
在此以常用工况 50FFB、64ODB、50MDB 为例,结合相应的试验数据,经过校核有限元模型中零部件的几何形状、材料和厚度,调整台车与整车的相对位置,利用RADIOSS 有限元软件进行计算,得到对标分析结果。
壁障台车信息
RADIOSS 格式的偏置碰固定壁障为solid 壁障,总质量为26.1kg,节点总数为49180,单元总数为48311,其中壳单元总数为9310,实体单元总数为39000,并包括一个刚体单元。
RADIOSS 格式的侧碰可移动变形壁障总质量为 950kg,其中分为前面碰撞块 24kg,台车 926kg。模型的基本信息中,节点总数为8629,壳单元总数为348,实体单元总数为6300。
能量信息
在整车仿真计算过程中,主要包括的物理能量有动能、内能、沙漏能、接触能等能量信息。从图4 可以看出,整车 50FFB 正面碰撞使用 RADIOSS 计算仿真过程中,整个模型的物理能量保持平稳下降趋势。动能和内能的变化也处于合理状态之中,沙漏能占总能量的3.7%,接触能量占总能量的14%。
核反应堆元件必须无懈可击
上海电气核电设备有限公司(以下简称:上海核电)是我国第一家核岛一级容器设备制造企业,曾先后承制了秦山一期核电站反应堆压力容器、蒸发器和稳压器、出口巴基斯坦恰西马核电站蒸发器和稳定器、清华大学高温气冷堆压力容器以及秦山二期核电站压力容器、稳压器和蒸发器等。
反应堆压力容器是用来固定和包容堆芯及堆内件的封闭容器,可使核燃料的链式裂变反应限制在一个封闭的金属壳内进行。如果说燃料元件包壳是防止放射物质外逸的第一道屏障,压力容器则是防止放射性外逸的第二道屏障。在高温、高压、强辐射与强腐蚀的条件下必须能可靠的持续工作 40 ~ 60 年。
反应堆压力容器进口接管和出口接管是压力容器的主要部件,在核裂变状态下产生的核能通过进口接管和出口接管传递给蒸发器进行能量传递。进口接管和出口接管为圆柱型筒表面,必须承受非常高的温度和压力。此类元件设计难度高,尤其是与压力容器连接的部分——进口接管、出口接管和反应堆压力容器连接部分是由三个相贯面组成的特殊曲面,因形状酷似马鞍,业内俗称马鞍形曲面。马鞍形曲面对设计和测量带来一定的难度。
过去,上海核电必需委托第三方企业代为加工反应堆压力容器的进口接管和出口接管,不仅外包的费用昂贵,单件加工费用高达几十万元。“加工周期长,加工质量难以完全控制,”上海核电首席技师李治国说。“一旦对方加工出错造成工件报废,就会严重拖延反应堆压力容器的整体生产过程,造成用户合同延迟交货,带来相应的经济和商业信誉的损失。”
基于 NX 的数字化工厂
上海核电管理层决定斥资引进目前世界上更先进的数控加工设备,又引进了当今更先进的计算机辅助设计 (CAD) 和计算机辅助制造 (CAM) 解决方案—— Siemens PLM Software 的 NX™ 软件。
在新流程中,在 NX 中完成部件建模。 NX CAM 被用来从 NX 部件模型中直接为刀轨编制编程。然后进行仿真机床排序。仿真过程中出现的错误将被修正,然后在机床上加工部件。“整个过程中,仅使用 NX 一个平台,”李治国说。“ NX CAM 输出 NC 数据,以驱动由 Siemens SINUMERIK 840D 控制的机床,从而实现 CAD-CAM-CNC 全集成流程链。”
因为反应堆压力容器进口接管和出口接管的结构相似,只是尺寸不同,所以在 NX 的建模阶段,就采用全参建模,对关键模型参数通过表达式赋值,这样在对其他同类型的接管,只需要建立一个模型,当涉及到其他模型尺寸发生变化时,就可以通过更改少数表达式的数值快速建立新的三维模型。“这样可以尽量减少重复工作,”李治国说。
解决了马鞍形面问题
使用 NX CAM 仿真机床操作是新流程不可或缺的组成部分,也是公司认为成功的关键步骤。使用 NX 的组装建模功能,可在屏幕上将一个部件的数字模型和相关的工装夹具组装起来。
使用 CAD 的各种功能,可在 NX 中设计出部件和相关工装夹具的三维模型。与机床和控制器相匹配的 NC 程序 G 代码在 NX CAM 中界定。使用机床的实际运动三维仿真,在 NX CAM 中检查和验证 NC 程序。检验有无干涉碰撞,加工时有无超出行程范围,有无出现欠切、过切现象。有了 NX CAM ,即可将实际加工时遇到的问题在加工前全部消除掉。
对于上海核电来说, NX 较重要的功能是:支持设计自动化(可以重复使用已掌握的知识)。被公司称为“加工格式”的模板在生成后,即可捕获每条接管的各种设计和生产参数。一旦明确了新接管的独特设计细节——如具体的尺寸、形状等,数分钟内 NC 程序便会更新,生成一个完整且经过验证的 NC 代码。由于 NX CAM 中集成了后处理程序,与具体的机床和控制器匹配,因此可以随时优化 NC 程序与 G 代码。模板中界定了经过验证的设计和生产参数,整个设计和生产过程既安全又可靠。
通过这个基于 NX 的全新设计制造集成流程,上海核电解决了过去为其带来麻烦的马鞍形面问题。事实上,该流程使得公司可以采取独特的方式生产此类部件。本需在多台设备上完成的各种不同操作,现在只要一台立式轧机即可。“据我们所知,这种方法在国外市场也是史无前例的,上海核电是第一家,”李治国说。 NX 足以支撑直径 10 英尺( 3.15 米)的立式轧机的运行,省去了多个固定装置,并改善了以往的操作步骤,减少了劳动量。
自从运用了 NX ,马鞍形曲面的开发周期从 1 个月缩短至 4 天(约 40 个工时)。而过渡圆角的开发周期则从过去的 18 天缩短至现在的不足 8 天。李治国说:“这些成果具有非常重大的意义。”
李治国补充道:“之所以项目进展如此顺利,是因为 NX 系统为我们提供了一个很好的实现平台,我们所有的要求都得到了 NX 的完美支持,这一点非常关键。”
西门子和上海核电的此次合作,为高难度部件的生产走出了一条全新的道路。“ NX 终结了此类部件外包生产的历史,”李治国说。“我们现在能够自主生产此类部件,对复杂部件制造流程的了解提高了我们的创新能力。”
结论
本次模型转换基于某项目整车模型,详细阐述有限元模型从LS-DYNA 向RADIOSS 的基本流程以及转换方法,并利用该方法成功实现整车碰撞模型的转换,证明了此转换方法的可行性。RADIOSS 格式整车模型仿真计算结果与整车试验测试数据相比较的结果表明,仿真计算结果中整车结构变形模式和整车加速度曲线与实验测试数据具有良好的一致性。从而再次证明此模型转换方法和基本流程以及RADIOSS 模型求解器运用于整车碰撞计算的有效性。