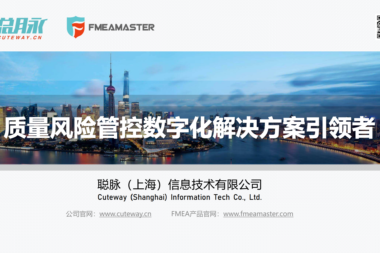
笔者曾经辅导过多家整车和零部件企业的DFMEA编制,涉及的产品包括系统、子系统和零部件级的各种产品100多种,现将多年的心得体会总结如下:
一个产品
产品一般可分为系统、子系统和零部件三个级别,做DFMEA分析前,需要先做产品结构分析,编制出这个产品的“产品树”,“产品树”上的每个节点需要编制一份对应的DFMEA表,所有的DFMEA表合在一起就构成了这个产品完整的DFMEA分析。如下图就是一个深沟球轴承的树形图,图中的每个节点就需要一份DFMEA分析表。
两种界面
具体一个产品的DFMEA分析时,首先要确定分析的边界,可以借助“框图”这个工具进行分析。产品的内部零件画在“框图”内部,与该产品有关联的外部产品画在“框图”的周边,再用线条将有连接的产品连起来,配合不同的线条样式和箭头样式代表不同的连接关系。“框图”内部的连接关系称为内部界面,“框图”内部的零件与外部产品或外部影响因素的连接关系称为外部界面。产品的内部零件、内部界面和外部界面是产品功能实现的基础,也是DFMEA分析的基础。如下图就是深沟球轴承的界面图:
三条假设
DFMEA关注的是产品设计的分析,为了不将分析的思路偏移正确的方向,有三条重要假设:
假设一:假设产品的零部件质量是合格的
假设二:假设产品的制造装配过程是合规的
假设三:假设相关人员的工作是没有犯错的
四类人员
DFMEA的小组构成很重要,直接关乎到DFMEA工作质量,核心小组成员人数控制在4~8人比较合适,需要以下四类人员参与:
项目组长:负责项目团队的成立、组织协调、任务分配和跟踪等工作,需要较强的组织能力和沟通能力;
技术专家:具备丰富的该类产品设计经验和扎实的技术功底,负责技术问题的把关;
相关方:包括质量、售前、售后、生产、采购、物流等相关人员,需要他们站在各自的角度提供输入信息和参与分析。
辅导员:深刻理解DFMEA的方法论,在分析过程中辅导其他人员按照正确的思路进行分析。
五个时机
DFMEA是动态文件,在以下5个时机时需要进行编制或重新分析:
时机一:新项目开发时
时机二:应用环境发生变化时
时机三:发生工程变更时
时机四:发生质量问题时
时机五:定期评审DFMEA时
六个步骤
以下六个步骤也将是FMEA第五版特别推荐的方法路径,特别是对于较复杂的产品按照这个路径几乎是必须的。
STEP1:定义范围,明确项目的边界,确定分析的对象和范围。
STEP2:结构分析,分析产品的内部组成及内外部关系,为后续分析做好准备。
STEP3:功能分析,收集和梳理顾客的需求,转化为技术的语言来描述。
STEP4:失效分析,与产品的结构和功能进行关联,结合历史数据进行失效原因分析。
STEP5:风险分析,对严重度、频度和可探测度进行量化打分,评估风险。
STEP6:措施优化,针对高风险的项目制订改进措施,进行优化提升。
七类错误
以下七类错误是经常发生的:
错误1:分析对象不清晰
错误2:功能/要求罗列不全
错误3:失效模式、后果和原因的描述错乱
错误4:原因分析不到位、不全面
错误5:原因分析偏离设计主题
错误6:现行预防措施与现行探测措施混淆
错误7:打分不准确
八项原则
DFMEA的实施是一项非常困难的系统工程,需要必要的资源支持,以及人员、制度、方法等多个因素的有效配合才能确保成功,可表述为以下八个原则:
原则1:领导重视
原则2:充分培训
原则3:跨功能小组协作
原则4:充分收集输入信息
原则5:建立知识库
原则6:建立作业规范
原则7:纳入项目评审要求
原则8:与问题解决直接关联
九大收益
做好DFMEA可以让企业在很多方面受益,比如:
收益1:利于沟通
收益2:沉淀知识
收益3:排查错因
收益4:预防问题
收益5:培训新人
收益6:加速开发
收益7:减少浪费
收益8:保证质量
收益9:客户满意